Sensor
Errors
A vendor that accepts credit
then returns money when a selection is made instead of vending the
product indicates a sensor error. The display message typically
states “PLEASE MAKE ANOTHER SELECTION.” Access the sensor error
codes by pressing * with the door open. The display will first
show the most recent error code #, followed by a set of
calibration numbers and finally the time and date in military
format. These readings will alternate on the display. Press * to
advance to the next error code. Record this information, which may
be useful when calling for assistance. The sensor error codes can
be cleared by calibrating the sensor with (Option
5). Refer to section 5 for trouble shooting
information.
back to
top
Health and Safety Errors
Machines vending perishable
products must be equipped with control software that contains the
Health & Safety (H&S) function. The H&S function is
activated automatically by setting
the temperature to 41°F or lower. Upon pressing the *
key to save the temperature setting, the control will beep and
display the state of the H&S function. The most important
feature of the H&S function is an error flag that, if
triggered by unsafe conditions, will disable all MDB devices and
prevent the machine from vending any product. This protects the
consumer from purchasing spoiled product.
As of this writing, the NAMA
specifications for perishable food product vendors require that
the temperature in the vendor must cool to 45°F within 30 minutes
of closing the door, and to 41°F within 45 minutes of closing the
door. This is to allow a recovery period following loading. After
this requirement has been met, the temperature in the vendor must
not get above 45 F or 41°F for more than 15 minutes at any
time. The H&S software allows the refrigeration cut-in
temperature to be set as low as 39°F. The refrigeration unit will
cut out at a temperature 5°F below the cut-in
temperature.
Unless otherwise specified
by regulatory agencies, AMS recommends a cut-in temperature of
39°F when vending perishable food products. The H&S software
includes additional logic to protect against evaporator freeze-up
by sensing the rate of cooling. If the rate of cooling drops below
2°F per hour, the compressor will be shut off for 5 minutes to
allow for defrosting. At the end of this time period, if the
temperature has exceeded 45°F, the control will allow the same
recovery period that is allowed after loading.
The error messages triggered
by unsafe conditions are described below. Once the error flag has
been set, it can only be reset by entering the service mode. This
is done by pressing the mode switch on the control board. It is
important for anyone servicing the vendor to observe any message
showing on the display before opening the door and unknowingly
resetting the error flag by entering the service mode to perform
another service function.
The H&S function can be
tested by manually warming the temperature sensor to simulate the
failure conditions. test
H&S function
back to
top
Out of
Service –
Temperature
Exceeded
This error occurs because
the temperature inside the vendor exceeded 45°F or 41°F for more
than 15 minutes (other than during the pull-down period following
loading). At the same time, the following message will be
displayed: “OUT OF ORDER (1), MAXIMUM TEMPERATURE EXCEEDED.”
Press the yellow service
mode switch, located on the lower right corner of the control
board, to clear the error after correcting the cause of the error
and discarding any food products that may have spoiled.
back to
top
Out of
Service –
Time
Exceeded
This error occurs because
the temperature inside the cabinet did not reach 45°F within 30
minutes or 41°F within 45 minutes of closing the door. If this
time limit is exceeded, the H&S error flag will be triggered
and the following message will be shown in the digital display:
“OUT OF ORDER (2), TIME EXCEEDED.”
Press the yellow service
mode switch, located on the lower right corner of the control
board, to clear the error after correcting the cause of the error
and discarding any food products that may have spoiled.
back to
top
Out of
Service
– Switch
Error
"OUT OF ORDER (3), DOOR
SWITCH" error occurs because the door switch was open for more
than 30 minutes, preventing the refrigeration unit from running
during that time. Press the yellow mode switch, located on the
lower right corner of the control board, to clear the error after
correcting the cause of the error and discarding any food products
that may have spoiled.
back to
top
Testing the H&S Function of the
Machine
Place unit in “Service”
mode. Press 8 to set the refrigeration cut-in temperature.
The temperature will be displayed in both Celsius and Fahrenheit.
Press 1 to increase the cut-in temperature. Press 2
to decrease the cut-in temperature. Press * to save and return to
OPTIONS.
Testing the H&S function is performed
as follows:
1. Place unit in “Service”
mode. Scroll to OPTIONS and press 8 to
display the set temperature of the unit. Press * to see if
the H&S option is enabled. Set point of the vendor must be
43°F or lower for the H&S option to be enabled.
2. At this point, the sensor
can either be disconnected, causing the controller to assume a
temperature of 255°F/124°C, or temporarily relocating the sensor
to the outside of the cabinet by removing the two (2) mounting
screws. Relocating the sensor will allow the sensor to be tested
as well. view
relocation
3. If the sensor is
relocated outside the door, close the door and allow the sensor
temperature to exceed the 45°F temperature setting. The
temperature of the sensor can be monitored by pressing * on the
keypad.
4. After 30 minutes, the
display should read “OUT OF ORDER (2), TIME EXCEEDED”. The machine
will not vend products until the door is opened and the controller
is reset.
5. Remount sensor inside
cabinet, insuring sensor wire is not caught or pulled. If the
sensor was disconnected, reconnect it at this time.
6. Close vendor door. The
vendor will return to normal operation.
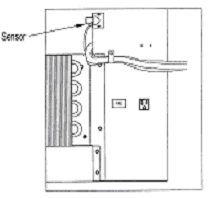
back to
top
Machine Errors
Top Level Error
Codes
To check for errors, enter the “Service”
mode by pressing the yellow service mode switch, located at the
lower right corner of the control board, while the door is
open. The controller will first scroll through the TOP
LEVEL ERROR CODES. If there are no errors, the
controller will display “NO ERRORS.” Otherwise, each Top
Level Error will be displayed for two (2) seconds. The error
messages automatically scroll for 30 seconds or until the # key is
pressed.
TOP LEVEL SERVICE ERROR CODES |
DISPLAY |
ERROR
DESCRIPTION |
JAM
MOTOR |
Motors
jammed |
DOORSWITCH |
Door switch open
greater than 1 hour |
SEL
STUCK |
Keypad character
closed greater than 2 minutes |
CHANGER |
Coin mechanism
error |
BILL
VAL |
Bill validator
error |
CARDREADER |
Card reader
error |
BT
DT |
Bottle
sensor |
back to
top
Sub-Level Error
Codes
To view the
SUB-LEVEL ERROR CODES, press the * key while the Top
Level Error Code is being displayed. Correcting the error
will clear the error code and display the next error code.
Once all errors are cleared, “SERVICE” will be displayed briefly,
then the first Service mode function is displayed.
back to
top
Jam
Motor
The display will
scroll each individually JAMMED MOTOR on the display for
two (2) seconds. Clear any jammed products from the
indicated vend columns. Use caution when freeing jammed
product (see 2.2.4 Helix Motion and Jamming). To reset the
error, select the jammed motor with the keypad. The control
will attempt to run that motor. If the motor runs
successfully, the control will display that selection followed by
“OK.” If the motor has been taken out of the motor matrix,
it will be re-established in the matrix. When all motors
have been re-established in the matrix, the display will read “ALL
OK.”
JAM MOTOR ERROR CODES |
DISPLAY |
ERROR
DESCRIPTION |
XX
JAM |
Jammed Motor =
XX |
ALL
OK |
All configured
motors are in the matrix |
XX
OK |
Selected motor
was already in the matrix |
back to
top
Doorswitch
The DOORSWITCH
error code has no sub-levels. If the Door Switch is reset by
closing the door, the error will reset itself.
back to
top
Sel
Stuck
Free up the indicated
selection button to clear the error. If necessary, loosen
the plastic escutcheon slightly from inside the door to free any
trapped foreign material that may be causing the button to
stick.
SELECTION STUCK ERROR CODES |
DISPLAY |
ERROR
DESCRIPTION |
X
STUCK |
Selection ‘X’ is
stuck |
back to
top
Changer
Press * to
scroll through the CHANGER error codes. Reference the
owner’s manual for your device for information on correcting
device errors.
CHANGER ERROR CODES |
DISPLAY |
ERROR
DESCRIPTION |
COMMUN |
Communications
error |
SENSOR |
Sensor
error |
CHUTE |
No coins
accepted for TBD time period |
JAM
TUBE |
Tube
jam |
CHK
SUM |
Check sum
error |
back to
top
Bill
Val
Press * to
scroll through the BILL VALIDATOR error codes.
Reference the owner’s manual for your device for information on
correcting device errors.
BILL VALIDATOR ERROR CODES |
DISPLAY |
ERROR
DESCRIPTION |
COMMUN |
Communications
error |
STK
FULL |
Stacker
full |
MOTOR |
Bad stacker
motor |
JAM
BILL |
Bill
jammed |
CHK
SUM |
Check sum
error |
OPEN
BOX |
Open
box |
SENSOR |
Sensor
error |
back to
top
Cardreader
Press * to
scroll through the CARD READER error codes. Reference
the owner’s manual for your device for information on correcting
device errors.
CARD READER ERROR CODES |
DISPLAY |
ERROR
DESCRIPTION |
CRD
ERR |
Card
error |
INVA
CRD |
Invalid
card |
TAMPER |
Tamper
error |
TDB |
Manufacturer’s
defined error |
COMMUN
4 |
Communications
error |
SERVICE |
Needs
service |
READ
ERR |
Reader
failure |
COMMUN
9 |
Communications
error |
JAM
CARD |
Card
jammed |
back to
top
BT DT
(Bottle Sensor)
The BT DT error code
has no sub-levels. Check/clear vend hopper, sensor and wire
connections.
back to
top
Water
Formation in the Cabinet
WATER FORMATION in
the cabinet indicates an air leak which allows moist air to
continually enter the cabinet and condense on the
evaporator.
1. Make sure the
refrigeration unit cover gasket is sealing properly all the way
around. In particular, check the opening where the refrigeration
lines pass through the cover. This opening should be sealed
completely around the lines with the gray putty very similar in
consistency to modeling clay
2. Make sure the door
is properly tightened so that it makes contact with the gasket on
all sides.
3. Make sure there are
no foreign objects interfering with the vend door, and the vend
door closes properly.
back to
top